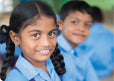
This order will fund a child to learn to read and write near our factories for
You have no notifications.
Your Cart
This order will fund a child to learn to read and write near our factories for
Increase your impact and add one of our luxury staples to your order:
Freya T-Shirt
£20
Abbey Vest
£18
Freya V-neck T-Shirt
£20
Adding to your cart...
These measurements are of this specific item, not your body, so are much more detailed. For generalized size information please visit the Body tab above.
There can be variation in the sizing due to fabric tolerance and weight so please bear this in mind if your measurements don't look right and if in doubt go for your standard size. You can see how an item looks on a range of heights and sizes on the Model Sizes tab.
Measure a similar style item that fits you well and compare, and you should get a good guide. We always recommend double checking so you get the right fit for you. Some of our pieces are designed to be a snug fit, while others are boxy or floaty, so you might want to go smaller or larger depending on the look you prefer.
Still need help with sizing? Get in touch with support@thisisunfolded.com or use our live chat!
As we only produce clothes based on what people order, instead of ordering multiple sizes to try, we are here to help you pick the right size before you order.
Where an item is available in two lengths we suggest if you're under 5ft 3 (161.5cm) you go for the short option. You can filter sizes below as well.
Garment Sizing
CM
Inches
Check back soon for additional size information
At Unfolded we follow a standardised guide for core body measurements, this is in line with standard sizing from a lot of the major UK high street retailers. Meaning, that if you buy a size 12 dress at other brands, then you will normally be a size 12 with us!
To help you find the right size we offer a handy measurement guide for each individual garment so you can compare the individual fit and size for each style - this is available in the garment tab.
All of our clothes are designed to look great on a range of sizes and body shapes and we’re happy to help make sure you get the right fit. If you have any questions about sizing then please feel free to use our live chat or email us on - support@thisisunfolded.com.
CM
Inches
How to measure yourself
To choose the correct size for you, we suggest measuring your body as follows:
Bust: Measure around the fullest part whilst wearing a bra that fits you nicely
Waist: Measure around your natural waistline
Hips: Measure 20cm down from your natural waistline
When you get a new dress, how often do you think about the journey it’s taken to get to you? Probably not much - but that's not your fault. Brands don’t exactly scream and shout about it!
We do things differently at Unfolded, and we want you to know and understand more about the process. From rolling out the fabric all the way to your order arriving on your doorstep, we’ve outlined each and every step.
Why? The more you know, the more the work that goes into each item by hard-working people across the world is appreciated, and when you appreciate your clothing you give it more love.